Bluetooth-Controlled Vehicle
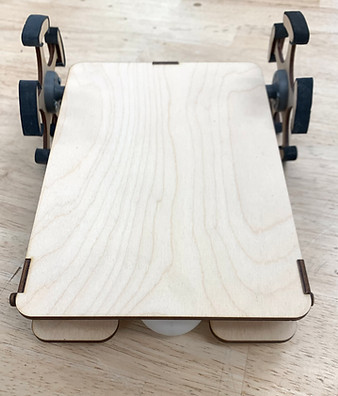
Children enjoy playing and racing with their remote-controlled cars. Cars race through wild obstacle courses to ultimately demonstrate the champion. These experiences create moments of entertainment, stress, and friendships. In UC Berkeley’s Prototyping and Fabrication course, students delved deep into understanding the mechanism and processes behind bluetooth-controlled vehicle in this project, and ways to make its design, shape, and structure optimal to withstand a variety of surfaces and environments.
Duration
November 2022 - December 2022
Roles
-
Learned vehicle structure and motion principles, including wheel mechanics and their impact on performance.
-
Applied modularity, functionality, and simplicity for effective design.
-
Built low-fidelity prototype to test electronics and Bluetooth functionality.
-
Designed vehicle by hand and in Adobe Illustrator.
-
Laser-cut and assembled high-fidelity prototype.
Skills
-
Diligent design planning
-
Value of modularity, functionality, and simplicity
-
Clear vision
-
Knowledge of modular design
-
Skillful prototyping
-
Creative handrcrafting and laser cutting
Design Challenge
Design a vehicle that focuses on functionality and mounting methods (modularity), with all parts/components secured consisting of clear joints. The bluetooth-controlled vehicle should be prepared to drive through an obstacle course with varied terrains and a four-to-one incline slope.
Evolution of Design
Phase 1: Low-Fidelity Prototype
We designed a low-fidelity prototype using basic parts such as a cardboard box, electronics, and provided wheels. However, we faced challenges with the electronics and Bluetooth connection, which initially prevented the vehicle from moving. After troubleshooting and making necessary replacements, we achieved the vehicle's movement. The low-fidelity prototype allowed us to gain insight on the vehicle’s mechanism and processes, which helped inform our high-fidelity design.

Phase 2: High-Fidelity Prototype
Initial Sketches and Brainstorming


Later decided to make the solo third wheel a rolling ball
After discussion, chose Option 4-
gapped wheels with “feet”

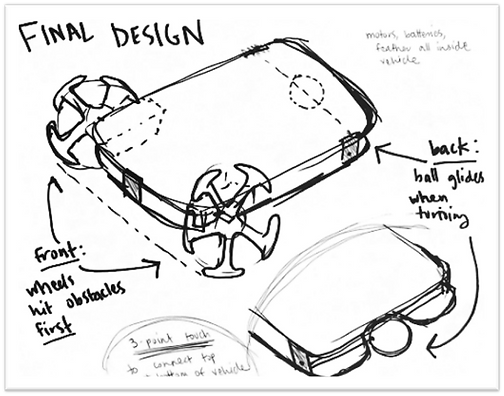
Final Sketches

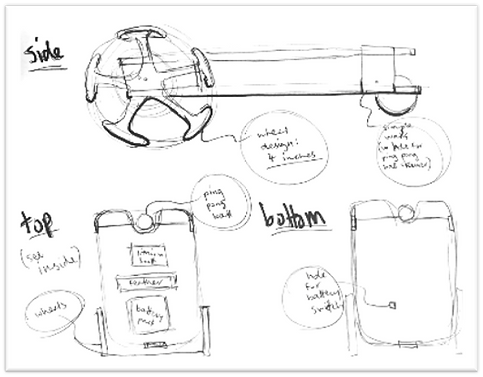
High-Fidelity Prototype
Design Process Description
Designing
-
Rounded parts to prevent breakage.
-
Created an opening for easy battery switch access.
-
Provided wheels with a 3 cm gap between "feet" for varied surfaces.
-
Enhanced wheel stability by adding separate "feet" while minimizing weight.
Constructing
-
Securely attached wheels using 3D-printed connectors.
-
Utilized snap-fit joints for easy disassembly.
-
Centered major weight, like the battery pack, for improved speed.
Vehicle Design Description
​The bluetooth vehicle design is simple, intentional and multi-functional:
Simple
The vehicle is made of laser-cut plywood, and all other parts (wheel connector, rubber bands, wooden skewer, ping-pong ball) were found materials.
Intentional
The body is thin and wide, and fit to the motor’s height. The body’s size is no larger than needed to hold all electronics.
Multifunctional
Side connectors that hold the top and bottom of the body together also hold the skewer that the ping-pong is placed through.
Adobe Illustrator Sketches




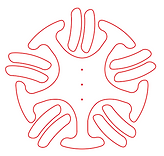
Process Photos
Assembly


Bluetooth Testing
Final Prototype Photos
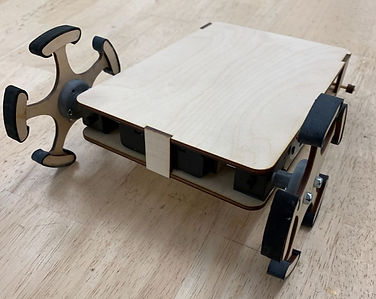
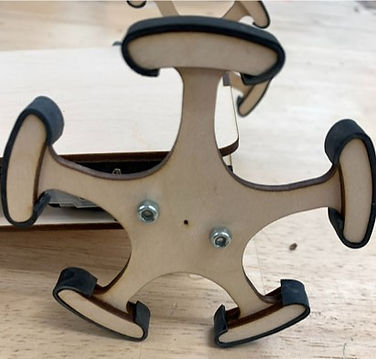
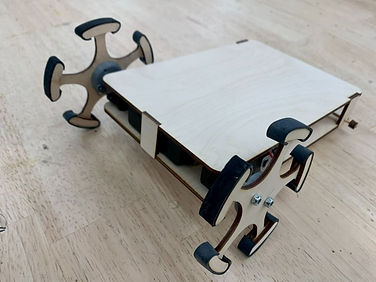


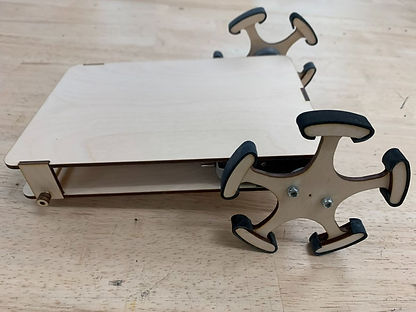
Process Reflection
Frustrations Encountered
The main difficulties we encountered were during the initial phases of the project.
-
It took us a lot of time, commitment, and dedication during Part 1 of this project, where we had to make sure all the electronics were working, and that the Bluetooth was connecting.
-
After several days and multiple tries, the code was finally working, and we were able to connect the electronics to Bluetooth to achieve a moving vehicle!

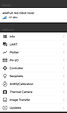
Brainstorming Process
-
At first, it was a little difficult to envision the most optimal vehicle design.
-
Initially, we were planning to design a vehicle with just 2 wheels, but we decided to go for a third “wheel” that would help the vehicle with steering and gliding along different surfaces.
-
With thoughtful brainstorming, we decided to design the vehicle’s wheels to have gaps between their “feet” so that they could withstand various surface types for the obstacle course.
-
Additionally, we designed the vehicle’s body to be wide and low to the ground for quick speed and movement.
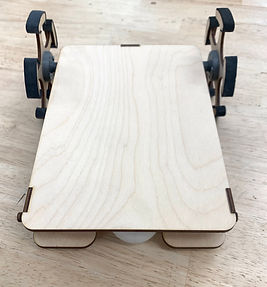
Lessons Learned
Modularity
We prioritized functionality and modularity to the vehicle design.​
-
Facilitated easy part replacement.
-
Wheels attached with nuts and screws.
-
Snap-fit top for electronics access.
-
Secure golf ball and skewer with wooden washers.
Simplicity
We learned that simplicity is key to design.​
-
Utilized household items for motion.
-
Added strength with stacked wheel feet.
-
Achieved smoother movement with rubber bands.
